ABSTRACT
Techno Rice, which is the rice treated with the state of the art supercritical carbon dioxide rice cleaning process, is tasty, clean, safe, and environmentally sound. As for the preparation of boiled brown rice, no additional rinsing and presoaking is needed and requires much less cooking time as well. In the meantime, it retains the fragrant and savory characters of rice with added remuneration of dietary fiber, antioxidants, and polyols which include: ferulic acid, its esterified derivatives (oryzanols), tocopherols and other phenolic compounds. The result shows that the partially defatted rice is more palatable and healthier, and it has longer shelf life. Furthermore, the process can remove pesticides residues, reduce microbe content and destroy existing insect and insect eggs to make consumption of the rice safer than ever. Techno Rice is tasty, healthy, safe and surely an alternative to compete with other products in the global rice market.
Keywords: Supercritical Carbon Dioxide, Techno Rice, Brown Rice
INDTRODUCTION
Supercritical fluid technology has been applied in industries for more than twenty years. Its first industrial application was on the extraction of hop resin, and in the1970’s it was used to decaffeinate coffee beans in Europe. Although there is considerably high number of works being tested in various applications, in the end of twentieth century, the supercritical fluid technology does not become the prospective industrial process yet as it was expected. Nevertheless, in the twenty-first century, it has been considered as one of the “Green Chemistry” processes. Unless it can be widely accepted by the industry, the very growth of this environmentally friendly clean process will be in jeopardy.
The research on this new technology in Taiwan is still insignificant in terms of governmental support and number of the researchers involved. Most of work adopting this technology focused on new applications in laboratory scale. The design of industrial apparatus and commercial process plant for supercritical fluid technology is rare. The first commercial plant for using supercritical carbon dioxide as cleaning solvent for rice, denoted as “Techno Rice”, was commissioned successfully in Taiwan in the end of 1999. It can be considered as the stepping-stone for the industrial application of the supercritical fluid technology in Taiwan.
Supercritical fluids extraction (SFE)
Supercritical fluids extraction, in most case, uses carbon dioxide as solvent and conducts extraction under its supercritical condition (McHugh, M. A., Krukonis, V. J., 1986). It contains all benefits of gaseous and liquid solvents, which are used in traditional chemical engineering unit operations. Carbon dioxide is non-toxic; it does not leave any residual side effects that may harm human bodies as other organic solvents may do. Supercritical carbon dioxide is a fluid in between the status of gas and liquid. It has high diffusivity, low viscosity, and non-flammable, and does not pollute and has high selectivity. It uses differences in temperature and pressure to adjust its fluid characteristics to help extraction technology becomes more flexible.
Basically, supercritical carbon dioxide technology raises the temperature and pressure of carbon dioxide to above critical level, utilizes its liquid-like solubility, gas-like diffusivity, viscosity and surface tension to expedite the extraction process. In other words, under supercritical conditions, carbon dioxide is able to penetrate into the solid matrix as gas and dissolve impurities in and on the matrix as liquid while “laundering” the rice.
In addition, supercritical carbon dioxide can be separated from extract easily, without having the solvent recovery by boiling up the washed-out organic solvent as a practice for traditional liquid extraction process. Therefore, it leaves no organic solvent residue, as we may consider the process as a dry cleaning process for the rice, and will not pollute environment in any way. SFE process fits perfectly into the basic principle for modern green processing technology.
Starting from the 60’s, many research groups, primarily in Europe and then later in the U.S., have examined SFE for “advance” extraction processes. European researchers emphasized extraction from botanical substrates, for example, spices, herbs, coffee, tea, and so on, uses predominantly supercritical carbon dioxide. By the 80’s there are several large SFE process plants in operation in Germany, UK and US, for decaffeinating coffee and tea and extracting flavors and essential oils from hops, spices, and herbs (Lack and Simandi, 2001.)
Ever since the launch of this new technology, the focus of supercritical fluids is on water, carbon dioxide and alcohol, because those are considered as green and sustainable in nature. It comes with no surprise that one application attempts to use supercritical carbon dioxide as a cleaning solvent to wash out the contaminants on a solid matrix. This is a sensational idea; however, would it worth using rather expensive technology on low-tech industry like rice milling, which has been considered cheap?
Supercritical fluid rice cleaning process (SFRCP)
This is a simple idea but the technology itself is not an easy task. Supercritical fluid rice cleaning process is a typical SFE practice emulating the pioneer SFE decaffeinating process that has existed for quite some time in coffee and tea industries. Generally speaking, supercritical fluid rice process (SFRCP) uses carbon dioxide under supercritical conditions to permeate into rice and dissolve possible pollutants from the surface and within (Lack and Simandi, 2001). SFRCP can also exterminate existing germs and insect eggs so that the rice is much cleaner and safer for human consumption.
The process is constructed with three 5.8 cubic meter extractors which operate cascades in series. Like most basic laboratory SFE unit, the main engineering design of this commercial apparatus consists of extractor, separator, pressure pump and heat exchanger (Fig. 1). In addition, a co-solvent pump is equipped for modification of polarity of the extraction solvent and supercritical carbon dioxide in this case.
A hermetic centrifugal pump is used as a booster pump to avoid cavitation to replace pre-chill water bath, which is a common practice in laboratory unit, for the sake of efficiency and spatial design. A 450 horsepower plunger pump, tandem with the booster pump, is capable of delivering 20,000 kg/hr. of liquid carbon dioxide and pressurizing operation pressure up to 350 bars (Fig. 2). An inclined tube bundle heat exchanger is used to heat up the pressurized liquid carbon dioxide to reach its critical temperature before entering the extraction vessel.
For recycling of the carbon dioxide at gaseous phase, after evaporation at the separator by means of pressure reduction and temperature increment, another tube bundle heat exchanger is used as an inline condenser during operation.
Carbon dioxide in the pressure vessel is then equilibrating with storage tank (working tank) which stores liquid carbon dioxide under its equilibrium vapor at temperature around 20 degree Celsius. A two-stage compressor is used at the final step for carbon dioxide recovery before opening of the extraction vessel. The compressor can deplete the gaseous carbon dioxide in the extraction vessel to 4.5 bars or lower to minimize carbon dioxide losses. As a result, the empirical data for average recovery of carbon dioxide is approximately 99.5%.
Co-solvent is introduced into the process by mean of a diaphragm pump before pressurized liquid carbon dioxide entering the pre-heater. Presumably, the surface area and the contacting time between carbon dioxide and co-solvent are sufficient to reach equilibrium and to become a single phase, by definition.
It is crucial to avoid any direct contact of rice with water, as it may present or precipitate inside the vessel as a second phase. Monitoring the stroke of the co-solvent pump and tuning the concentration of the co-solvent, SFRCP can further manipulate the moisture content of the rice. In the meantime, the shrinkage of the rice kernel must be prevented because carbon dioxide may take out the moisture from the rice and diminish the appearance as well.
Automatic controlling system, quick-acting closure design, safety sensor and interlock system have made the four-story SFE harboring operation plant which requires a minimum of two operators to keep it fully functional (Fig. 3). Extra precaution has been taken with a safety measure in mind; therefore, a touch screen control panel has been installed alongside the top and the bottom quick-acting closure for onsite operation and supervision (Fig. 4).
SFRCP is operated semi-continuously with three extraction vessels arranged in sequence. The supercritical carbon dioxide, with or without co-solvent, is entering the vessel from the bottom continuously. The three extraction vessels normally will operate in cascade mode, which can be divided into two different time periods, namely extraction time and down time. In doing so, we can save up to 1/3 of process time, in view of a single batch, by partially overlapping the extraction time period while two vessels are operated as a stringed extractors. In other word, while one vessel operates with high-pressure carbon dioxide the other two vessels are either depressurizing or ready for unloading and loading, or pressurizing and ready for in tandem with the existing vessel.
After the extraction, supercritical carbon dioxide can then be gasified by means of depressurization and evaporation in the separator. As the supercritical carbon dioxide has rendered its solvent power to gas phase, the water in oil emulsion precipitated in the separator can then accumulate and be drained out for further separation, which can be done easily by breaking up the emulsion with steam. Gas carbon dioxide is subsequently introduced into a washing column to strip away trace residue of contaminant that may be carried over before it is re-condensed into liquid form and drained down to the working tank.
The washing column is basically a countercurrent extraction packed column. To avoid overflow and for easy handling, the gas carbon dioxide, as continue phase, is ascending from the bottom and the hot water, as disperse phase, is dripping down from the top. Water level of the column is monitored automatically for depleting and replenishing.
Gas carbon dioxide escaped from the washing column and saturated with water is introduced into the condenser to conclude with the “laundering” cycle. Condensed water occurs as it passes through condenser and is collected from the bottom of the working tank; which is designed with 10-degree incline, and drains out automatically with a sensor monitoring level gauge.
The spent water, which is saturated with carbon dioxide, is introduced into a gas/liquid separator to deplete the gas carbon dioxide before coming into contact with micro filters and active carbon for further purification.
The hermetic centrifugal pump is designed to compress the liquid carbon dioxide effectively to about 14 bars higher than what it is in the working tank, which is equilibrated with the pressure of separator at around 55 bars. Theoretically, the centrifugal pump can be used directly as the pressure pump for the process. In fact, it is even more suitable than plunger pump for delivering massive liquid flow. However, it is never realistically feasible, as the pump has reached its limitation in terms of the diameter of the impeller and the length of shaft inside the stage casing.
Relatively speaking, plunger pump is still the number one choice for the industrialized commercial high-pressure process (Vetter et al., 2001). In practical, the reciprocal pump featured with three plungers and equipped with dampers to reduce pulsation is commonly used for most of the existing commercial SFE processes.
SFRCP has integrated seamless with the traditional rice milling process at a production capacity of 2 to 4 metric tons of rice per hour (Fig. 5). The utilities for the complete process have included air compressor, steam boiler and chiller, cooling tower, water treatment and rice transport system. Together with the main devices of the SFRCP the total electric energy requirement for the plant is around 1700kw. In other word, it can never be considered as an energy saving process if compared to traditional rice milling.
The techno rice
Techno Rice is named in comparison to organic rice, in a sense that the using of modern technology to ensure the treated rice has its quality assured like organic rice. Techno Rice has made the nutritious brown rice more palatable. It is worth mentioning that, the Techno Rice offers a greener, safer and technologically sound alternative, which gives consumers full peace of mind.
Supercritical fluid extraction itself can be called clean process or green technology. This technology reduces contaminants, such as pesticides, microorganisms and pests in the treated rice products to the minimum, retaining all the nutrients in the rice. SFRCP has changed the undesirable traits for brown rice those are not easy to store, cook, and roughness in eating. Techno Rice is aromatic, chewy, and leaving no coarsely mouth feel. As consumers become more aware of the food, they dwell on issues like nutraceuticals, functional ingredients, convenience, and safety; Techno Rice, especially brown rice, would be an excellent product to target this sophisticated market.
When it comes to a basic fact that although white rice is indeed tastier than brown rice, it comprises only a compact agglomeration of starch granule. Even though people are aware of nutritional values, nutraceuticals and functional ingredients in the brown rice, the pericarp, seed coat and nucellus that make up the caryopsis coat (bran) in brown rice have kept consumers away from being rational.
Rice bran contains most of the oil in the rice and covers the outer skin of rice grains with a waxy layer, hampering water absorption of the rice. To cook the rice, the starch granules need to absorb sufficient amount of water in order to swell up and rupture for the carbohydrate to be fully gelatinized. With the formation of the complex between free fatty acids, carbohydrates and protein plus the deferring of water absorption by its natural barrier, the rice has been referred to be poor in eating quality after cooking.
Brown rice is more susceptible to deterioration than white rice. Lipase, an extremely active enzyme underneath the bran, can hydrolyze rice lipid into free fatty acid as soon as the husking process begins. Free fatty acid can be oxidized to hydroperoxides and other smelly carbonyl compounds; which will produce off-flavor and form complex with starch and protein and accelerate the aging process of rice.
Techno Rice offers a simple solution for the problem by taking away deterioration elements as such. Supercritical carbon dioxide removes the waxy layer and fatty acid inside rice bran, prohibits the formation of polymer complex and prevents rice from aging.
Once the odor caused by oxidized fatty acid is removed, the genuine aroma of cooked rice can be released. In addition, SFRCP causes micro-fracture on the bran; consequently, Techno Rice can absorb water much more effectively. The soaking time can then be shortened and the process to swell and gelatinize starch during cooking can be expedited.
The result is a nutritious tasty brown rice, which is soft inside and chewy on the outer layer. It has been shown that SFRCP treated brown rice can be prepared similar to white rice without the need for overnight soaking which is a common practice in Taiwan. Apart from grainy texture, the outer skin has become chewier; the perception for the SFRCP brown rice is just as tasty and soft on texture as regular white rice. The average cooking time can be cut short by approximately 25% as well.
Similar to the carbon dioxide packaging, which is widely used for perishable dairy and meat products and rice storage for military usage as well, Techno Rice can sustain this practice as an additional benefit by a designed one-way valve on the bag (Fig. 6). As the chemical potential of the dissolved carbon dioxide in Techno Rice is much higher than that of its surrounding air, the carbon dioxide will gradually be released from the rice matrix.
Like what is commonly used in coffee bean packaging, a one-way valve has provided a conduit for the excess carbon dioxide to escape. Being different from the carbon dioxide that generates slowly in the coffee bean during storage, an enormous amount of carbon dioxide that has previously dissolved in the rice during SFRCP busts out and pops. In addition, the predominant carbon dioxide can expel the air in the bag and provide a strictly anaerobic storage environment for the rice. Since carbon dioxide can again dissolve back into the solid matrix and water in rice, after an empirical time period of 7 to 14 days, the package will then shrink automatically. It creates something similar to a vacuum package and results in an even better preservation system than traditional gas package or vacuum package alone.
The concentrated carbon dioxide dissolved in rice can produce carbonic acid, which can further reduce the pH value of rice to around 3, theoretically. Such acidic condition can further prohibit germination of microbes and pest eggs. Although the rice can never be completely sterilized by the process hitherto used, most of those hidden bio-contaminants can be further inhibited by the presence of carbon dioxide. Therefore, Techno Rice can be stored much longer, and even the most pest-prone brown rice requires no needs for commercial vacuum packaging.
CONCLUSION
With mounting pressure from the WTO to open market, rice industries in Taiwan are adapting the new technology to revive and fend them from the pending competition. Organic rice can certainly increase farmers’ income, as well as, provide consumers with a healthier and safer option for rice. Due to the facts that organic rice production is very labor intensive and has high production cost and other various factors, it has never been able to increase significantly and reach the magnitude as what has been anticipated. Furthermore, subtropical climate and over cultivated rice field have made it even more difficult for the farmer to achieve the organic farming criteria while maintaining commercially feasible production cost to compete globally.
The partially defatted rice, namely Techno Rice, is more palatable, healthier and has longer shelf life. The process can removes pesticides residues, reduces microbe content and destroy existing insect and insect eggs to make consumption of the rice safer than ever.
Techno Rice is tasty, healthy and safe and surely is an alternative to compete with variety of rice in the global rice market. It is commercially available in the Taiwan for the past fifteen years. How well this product can survive in the traditional rice market, locally as well as internationally, is still too early to determine. Nevertheless, it has exploring a new application of supercritical fluids technology on staple food for the Homo sapiens.
REFERENCES
Arai, Y., Sako, T., and Takebayashi, Y. (Eds.) 2002. “Supercritical Fluids – Molecular Interactions, Physical Properties, and New Applications.” Springer-Verlag, Berlin Heidelberg.
Lack, E. and Simandi, B. 2001. Supercritical Fluid Extraction and Fraction from Solid Materials. In “High Pressure Process Technology: Fundamental and Applications,” eds. A. Bertucco, and G. Vetter, pp 537 – 575. Elsevier Science B. V., Amsterdam.
McHugh, M. A. and Krukonis, V. J. 1986. “Supercritical Fluid Extraction – Principles and Practical.” Butterworths Publishers, Boston.
Stahl, E., Quirin, K. W., and Gerard, D. 1988. “Dense Gases for Extraction and Refining,” Springer-Verlag, Berlin Heidelberg.
Vetter, G., Luft, G., and Maier, S.. 2001. Design and construction of high-pressure equipment for research and production. Chapter 4 in “High Pressure Process Technology: Fundamental and Applications,” ed. A. Bertucco, and G. Vetter, pp 537 – 575. Elsevier Science B. V., Amsterdam.
.jpg)
Fig.1. 3D drawing of supercritical carbon dioxide rice cleaning system (SFRCP)
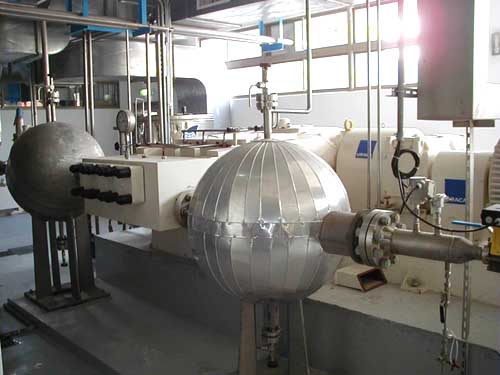
Fig. 2. High-pressure plunger pump equipped with dampers
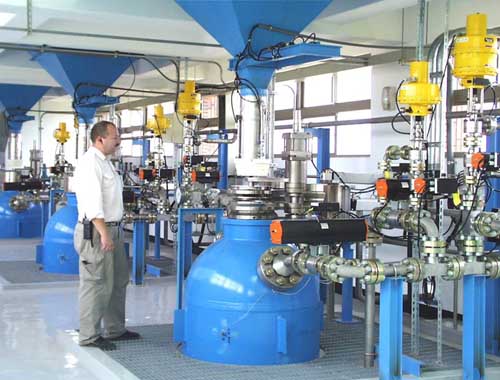
Fig. 3. Quick-acting closure at the top of the extraction vessel
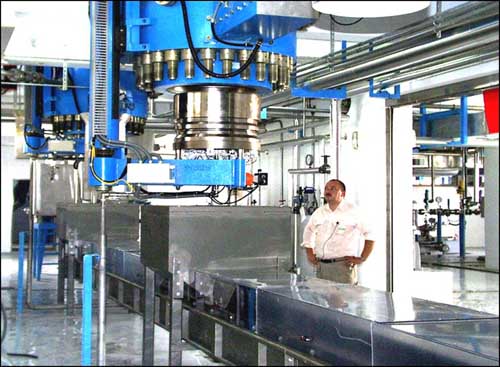
Fig. 4. Quick-acting closure at the bottom of the extraction vessel
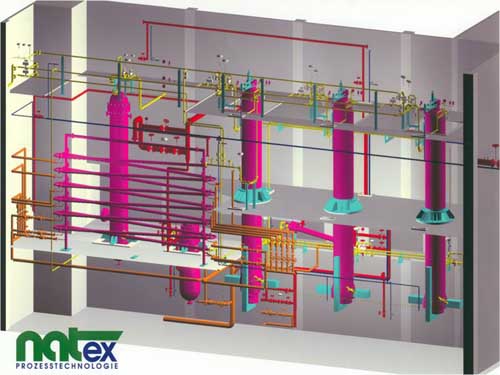
Fig. 5. Overview of SFRCP apparatus with three vessels arranged in series
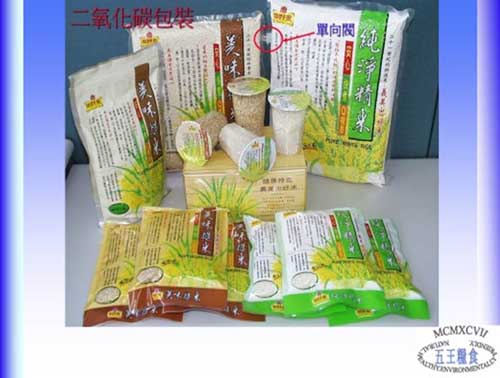
Fig. 6. Commercial SFRCP rice (Techno Rice) package with one-way valve.
Submitted for the FFTC-KU International Workshop on Risk Management on Agrochemicals through Novel Technologies for Food Safety in Asia, November 10-14, Sampran Riverside, Nakorn Pathom, Thailand |
The Techno Rice: An Industrial Application of Supercritical Fluid Technology in Taiwan
ABSTRACT
Techno Rice, which is the rice treated with the state of the art supercritical carbon dioxide rice cleaning process, is tasty, clean, safe, and environmentally sound. As for the preparation of boiled brown rice, no additional rinsing and presoaking is needed and requires much less cooking time as well. In the meantime, it retains the fragrant and savory characters of rice with added remuneration of dietary fiber, antioxidants, and polyols which include: ferulic acid, its esterified derivatives (oryzanols), tocopherols and other phenolic compounds. The result shows that the partially defatted rice is more palatable and healthier, and it has longer shelf life. Furthermore, the process can remove pesticides residues, reduce microbe content and destroy existing insect and insect eggs to make consumption of the rice safer than ever. Techno Rice is tasty, healthy, safe and surely an alternative to compete with other products in the global rice market.
Keywords: Supercritical Carbon Dioxide, Techno Rice, Brown Rice
INDTRODUCTION
Supercritical fluid technology has been applied in industries for more than twenty years. Its first industrial application was on the extraction of hop resin, and in the1970’s it was used to decaffeinate coffee beans in Europe. Although there is considerably high number of works being tested in various applications, in the end of twentieth century, the supercritical fluid technology does not become the prospective industrial process yet as it was expected. Nevertheless, in the twenty-first century, it has been considered as one of the “Green Chemistry” processes. Unless it can be widely accepted by the industry, the very growth of this environmentally friendly clean process will be in jeopardy.
The research on this new technology in Taiwan is still insignificant in terms of governmental support and number of the researchers involved. Most of work adopting this technology focused on new applications in laboratory scale. The design of industrial apparatus and commercial process plant for supercritical fluid technology is rare. The first commercial plant for using supercritical carbon dioxide as cleaning solvent for rice, denoted as “Techno Rice”, was commissioned successfully in Taiwan in the end of 1999. It can be considered as the stepping-stone for the industrial application of the supercritical fluid technology in Taiwan.
Supercritical fluids extraction (SFE)
Supercritical fluids extraction, in most case, uses carbon dioxide as solvent and conducts extraction under its supercritical condition (McHugh, M. A., Krukonis, V. J., 1986). It contains all benefits of gaseous and liquid solvents, which are used in traditional chemical engineering unit operations. Carbon dioxide is non-toxic; it does not leave any residual side effects that may harm human bodies as other organic solvents may do. Supercritical carbon dioxide is a fluid in between the status of gas and liquid. It has high diffusivity, low viscosity, and non-flammable, and does not pollute and has high selectivity. It uses differences in temperature and pressure to adjust its fluid characteristics to help extraction technology becomes more flexible.
Basically, supercritical carbon dioxide technology raises the temperature and pressure of carbon dioxide to above critical level, utilizes its liquid-like solubility, gas-like diffusivity, viscosity and surface tension to expedite the extraction process. In other words, under supercritical conditions, carbon dioxide is able to penetrate into the solid matrix as gas and dissolve impurities in and on the matrix as liquid while “laundering” the rice.
In addition, supercritical carbon dioxide can be separated from extract easily, without having the solvent recovery by boiling up the washed-out organic solvent as a practice for traditional liquid extraction process. Therefore, it leaves no organic solvent residue, as we may consider the process as a dry cleaning process for the rice, and will not pollute environment in any way. SFE process fits perfectly into the basic principle for modern green processing technology.
Starting from the 60’s, many research groups, primarily in Europe and then later in the U.S., have examined SFE for “advance” extraction processes. European researchers emphasized extraction from botanical substrates, for example, spices, herbs, coffee, tea, and so on, uses predominantly supercritical carbon dioxide. By the 80’s there are several large SFE process plants in operation in Germany, UK and US, for decaffeinating coffee and tea and extracting flavors and essential oils from hops, spices, and herbs (Lack and Simandi, 2001.)
Ever since the launch of this new technology, the focus of supercritical fluids is on water, carbon dioxide and alcohol, because those are considered as green and sustainable in nature. It comes with no surprise that one application attempts to use supercritical carbon dioxide as a cleaning solvent to wash out the contaminants on a solid matrix. This is a sensational idea; however, would it worth using rather expensive technology on low-tech industry like rice milling, which has been considered cheap?
Supercritical fluid rice cleaning process (SFRCP)
This is a simple idea but the technology itself is not an easy task. Supercritical fluid rice cleaning process is a typical SFE practice emulating the pioneer SFE decaffeinating process that has existed for quite some time in coffee and tea industries. Generally speaking, supercritical fluid rice process (SFRCP) uses carbon dioxide under supercritical conditions to permeate into rice and dissolve possible pollutants from the surface and within (Lack and Simandi, 2001). SFRCP can also exterminate existing germs and insect eggs so that the rice is much cleaner and safer for human consumption.
The process is constructed with three 5.8 cubic meter extractors which operate cascades in series. Like most basic laboratory SFE unit, the main engineering design of this commercial apparatus consists of extractor, separator, pressure pump and heat exchanger (Fig. 1). In addition, a co-solvent pump is equipped for modification of polarity of the extraction solvent and supercritical carbon dioxide in this case.
A hermetic centrifugal pump is used as a booster pump to avoid cavitation to replace pre-chill water bath, which is a common practice in laboratory unit, for the sake of efficiency and spatial design. A 450 horsepower plunger pump, tandem with the booster pump, is capable of delivering 20,000 kg/hr. of liquid carbon dioxide and pressurizing operation pressure up to 350 bars (Fig. 2). An inclined tube bundle heat exchanger is used to heat up the pressurized liquid carbon dioxide to reach its critical temperature before entering the extraction vessel.
For recycling of the carbon dioxide at gaseous phase, after evaporation at the separator by means of pressure reduction and temperature increment, another tube bundle heat exchanger is used as an inline condenser during operation.
Carbon dioxide in the pressure vessel is then equilibrating with storage tank (working tank) which stores liquid carbon dioxide under its equilibrium vapor at temperature around 20 degree Celsius. A two-stage compressor is used at the final step for carbon dioxide recovery before opening of the extraction vessel. The compressor can deplete the gaseous carbon dioxide in the extraction vessel to 4.5 bars or lower to minimize carbon dioxide losses. As a result, the empirical data for average recovery of carbon dioxide is approximately 99.5%.
Co-solvent is introduced into the process by mean of a diaphragm pump before pressurized liquid carbon dioxide entering the pre-heater. Presumably, the surface area and the contacting time between carbon dioxide and co-solvent are sufficient to reach equilibrium and to become a single phase, by definition.
It is crucial to avoid any direct contact of rice with water, as it may present or precipitate inside the vessel as a second phase. Monitoring the stroke of the co-solvent pump and tuning the concentration of the co-solvent, SFRCP can further manipulate the moisture content of the rice. In the meantime, the shrinkage of the rice kernel must be prevented because carbon dioxide may take out the moisture from the rice and diminish the appearance as well.
Automatic controlling system, quick-acting closure design, safety sensor and interlock system have made the four-story SFE harboring operation plant which requires a minimum of two operators to keep it fully functional (Fig. 3). Extra precaution has been taken with a safety measure in mind; therefore, a touch screen control panel has been installed alongside the top and the bottom quick-acting closure for onsite operation and supervision (Fig. 4).
SFRCP is operated semi-continuously with three extraction vessels arranged in sequence. The supercritical carbon dioxide, with or without co-solvent, is entering the vessel from the bottom continuously. The three extraction vessels normally will operate in cascade mode, which can be divided into two different time periods, namely extraction time and down time. In doing so, we can save up to 1/3 of process time, in view of a single batch, by partially overlapping the extraction time period while two vessels are operated as a stringed extractors. In other word, while one vessel operates with high-pressure carbon dioxide the other two vessels are either depressurizing or ready for unloading and loading, or pressurizing and ready for in tandem with the existing vessel.
After the extraction, supercritical carbon dioxide can then be gasified by means of depressurization and evaporation in the separator. As the supercritical carbon dioxide has rendered its solvent power to gas phase, the water in oil emulsion precipitated in the separator can then accumulate and be drained out for further separation, which can be done easily by breaking up the emulsion with steam. Gas carbon dioxide is subsequently introduced into a washing column to strip away trace residue of contaminant that may be carried over before it is re-condensed into liquid form and drained down to the working tank.
The washing column is basically a countercurrent extraction packed column. To avoid overflow and for easy handling, the gas carbon dioxide, as continue phase, is ascending from the bottom and the hot water, as disperse phase, is dripping down from the top. Water level of the column is monitored automatically for depleting and replenishing.
Gas carbon dioxide escaped from the washing column and saturated with water is introduced into the condenser to conclude with the “laundering” cycle. Condensed water occurs as it passes through condenser and is collected from the bottom of the working tank; which is designed with 10-degree incline, and drains out automatically with a sensor monitoring level gauge.
The spent water, which is saturated with carbon dioxide, is introduced into a gas/liquid separator to deplete the gas carbon dioxide before coming into contact with micro filters and active carbon for further purification.
The hermetic centrifugal pump is designed to compress the liquid carbon dioxide effectively to about 14 bars higher than what it is in the working tank, which is equilibrated with the pressure of separator at around 55 bars. Theoretically, the centrifugal pump can be used directly as the pressure pump for the process. In fact, it is even more suitable than plunger pump for delivering massive liquid flow. However, it is never realistically feasible, as the pump has reached its limitation in terms of the diameter of the impeller and the length of shaft inside the stage casing.
Relatively speaking, plunger pump is still the number one choice for the industrialized commercial high-pressure process (Vetter et al., 2001). In practical, the reciprocal pump featured with three plungers and equipped with dampers to reduce pulsation is commonly used for most of the existing commercial SFE processes.
SFRCP has integrated seamless with the traditional rice milling process at a production capacity of 2 to 4 metric tons of rice per hour (Fig. 5). The utilities for the complete process have included air compressor, steam boiler and chiller, cooling tower, water treatment and rice transport system. Together with the main devices of the SFRCP the total electric energy requirement for the plant is around 1700kw. In other word, it can never be considered as an energy saving process if compared to traditional rice milling.
The techno rice
Techno Rice is named in comparison to organic rice, in a sense that the using of modern technology to ensure the treated rice has its quality assured like organic rice. Techno Rice has made the nutritious brown rice more palatable. It is worth mentioning that, the Techno Rice offers a greener, safer and technologically sound alternative, which gives consumers full peace of mind.
Supercritical fluid extraction itself can be called clean process or green technology. This technology reduces contaminants, such as pesticides, microorganisms and pests in the treated rice products to the minimum, retaining all the nutrients in the rice. SFRCP has changed the undesirable traits for brown rice those are not easy to store, cook, and roughness in eating. Techno Rice is aromatic, chewy, and leaving no coarsely mouth feel. As consumers become more aware of the food, they dwell on issues like nutraceuticals, functional ingredients, convenience, and safety; Techno Rice, especially brown rice, would be an excellent product to target this sophisticated market.
When it comes to a basic fact that although white rice is indeed tastier than brown rice, it comprises only a compact agglomeration of starch granule. Even though people are aware of nutritional values, nutraceuticals and functional ingredients in the brown rice, the pericarp, seed coat and nucellus that make up the caryopsis coat (bran) in brown rice have kept consumers away from being rational.
Rice bran contains most of the oil in the rice and covers the outer skin of rice grains with a waxy layer, hampering water absorption of the rice. To cook the rice, the starch granules need to absorb sufficient amount of water in order to swell up and rupture for the carbohydrate to be fully gelatinized. With the formation of the complex between free fatty acids, carbohydrates and protein plus the deferring of water absorption by its natural barrier, the rice has been referred to be poor in eating quality after cooking.
Brown rice is more susceptible to deterioration than white rice. Lipase, an extremely active enzyme underneath the bran, can hydrolyze rice lipid into free fatty acid as soon as the husking process begins. Free fatty acid can be oxidized to hydroperoxides and other smelly carbonyl compounds; which will produce off-flavor and form complex with starch and protein and accelerate the aging process of rice.
Techno Rice offers a simple solution for the problem by taking away deterioration elements as such. Supercritical carbon dioxide removes the waxy layer and fatty acid inside rice bran, prohibits the formation of polymer complex and prevents rice from aging.
Once the odor caused by oxidized fatty acid is removed, the genuine aroma of cooked rice can be released. In addition, SFRCP causes micro-fracture on the bran; consequently, Techno Rice can absorb water much more effectively. The soaking time can then be shortened and the process to swell and gelatinize starch during cooking can be expedited.
The result is a nutritious tasty brown rice, which is soft inside and chewy on the outer layer. It has been shown that SFRCP treated brown rice can be prepared similar to white rice without the need for overnight soaking which is a common practice in Taiwan. Apart from grainy texture, the outer skin has become chewier; the perception for the SFRCP brown rice is just as tasty and soft on texture as regular white rice. The average cooking time can be cut short by approximately 25% as well.
Similar to the carbon dioxide packaging, which is widely used for perishable dairy and meat products and rice storage for military usage as well, Techno Rice can sustain this practice as an additional benefit by a designed one-way valve on the bag (Fig. 6). As the chemical potential of the dissolved carbon dioxide in Techno Rice is much higher than that of its surrounding air, the carbon dioxide will gradually be released from the rice matrix.
Like what is commonly used in coffee bean packaging, a one-way valve has provided a conduit for the excess carbon dioxide to escape. Being different from the carbon dioxide that generates slowly in the coffee bean during storage, an enormous amount of carbon dioxide that has previously dissolved in the rice during SFRCP busts out and pops. In addition, the predominant carbon dioxide can expel the air in the bag and provide a strictly anaerobic storage environment for the rice. Since carbon dioxide can again dissolve back into the solid matrix and water in rice, after an empirical time period of 7 to 14 days, the package will then shrink automatically. It creates something similar to a vacuum package and results in an even better preservation system than traditional gas package or vacuum package alone.
The concentrated carbon dioxide dissolved in rice can produce carbonic acid, which can further reduce the pH value of rice to around 3, theoretically. Such acidic condition can further prohibit germination of microbes and pest eggs. Although the rice can never be completely sterilized by the process hitherto used, most of those hidden bio-contaminants can be further inhibited by the presence of carbon dioxide. Therefore, Techno Rice can be stored much longer, and even the most pest-prone brown rice requires no needs for commercial vacuum packaging.
CONCLUSION
With mounting pressure from the WTO to open market, rice industries in Taiwan are adapting the new technology to revive and fend them from the pending competition. Organic rice can certainly increase farmers’ income, as well as, provide consumers with a healthier and safer option for rice. Due to the facts that organic rice production is very labor intensive and has high production cost and other various factors, it has never been able to increase significantly and reach the magnitude as what has been anticipated. Furthermore, subtropical climate and over cultivated rice field have made it even more difficult for the farmer to achieve the organic farming criteria while maintaining commercially feasible production cost to compete globally.
The partially defatted rice, namely Techno Rice, is more palatable, healthier and has longer shelf life. The process can removes pesticides residues, reduces microbe content and destroy existing insect and insect eggs to make consumption of the rice safer than ever.
Techno Rice is tasty, healthy and safe and surely is an alternative to compete with variety of rice in the global rice market. It is commercially available in the Taiwan for the past fifteen years. How well this product can survive in the traditional rice market, locally as well as internationally, is still too early to determine. Nevertheless, it has exploring a new application of supercritical fluids technology on staple food for the Homo sapiens.
REFERENCES
Arai, Y., Sako, T., and Takebayashi, Y. (Eds.) 2002. “Supercritical Fluids – Molecular Interactions, Physical Properties, and New Applications.” Springer-Verlag, Berlin Heidelberg.
Lack, E. and Simandi, B. 2001. Supercritical Fluid Extraction and Fraction from Solid Materials. In “High Pressure Process Technology: Fundamental and Applications,” eds. A. Bertucco, and G. Vetter, pp 537 – 575. Elsevier Science B. V., Amsterdam.
McHugh, M. A. and Krukonis, V. J. 1986. “Supercritical Fluid Extraction – Principles and Practical.” Butterworths Publishers, Boston.
Stahl, E., Quirin, K. W., and Gerard, D. 1988. “Dense Gases for Extraction and Refining,” Springer-Verlag, Berlin Heidelberg.
Vetter, G., Luft, G., and Maier, S.. 2001. Design and construction of high-pressure equipment for research and production. Chapter 4 in “High Pressure Process Technology: Fundamental and Applications,” ed. A. Bertucco, and G. Vetter, pp 537 – 575. Elsevier Science B. V., Amsterdam.
Fig.1. 3D drawing of supercritical carbon dioxide rice cleaning system (SFRCP)
Fig. 2. High-pressure plunger pump equipped with dampers
Fig. 3. Quick-acting closure at the top of the extraction vessel
Fig. 4. Quick-acting closure at the bottom of the extraction vessel
Fig. 5. Overview of SFRCP apparatus with three vessels arranged in series
Fig. 6. Commercial SFRCP rice (Techno Rice) package with one-way valve.