ABSTRACT
Smart Agriculture 4.0 Program of Taiwan targets three major fields, namely agriculture biotechnology, quality agriculture, and precision agriculture; precision agriculture is divided into two major categories: establishing foundations and promoting excellence. The current technical status of the aforementioned industries and post-promotion applications of the Smart Agriculture 4.0 Program for dairy farm are identified. The construction of production monitoring intelligent system and robotic milking operation parameterized wisdom network were carried out for research, development and application of pilot robotics. Based upon the performance data of Taiwan dairy herd improvement program (DHI) since 1978, an average of daily milk yield per head was 25.1Kg from 28,485 cows of 177 farms in 2018. Cow raw milk of DHI herds had the quality in average of 3.96% fat, 3.37% protein, 4.79% lactose, and somatic cell counts of 273 thousand cells/mL in 2018. DHI cows were 46.3% of 61,336 milking cows and DHI herds were 32.1% of 551 dairy cattle farms in Taiwan. Due to lack of young labors and enlargement of herd size, precision farming with robots is becoming an essential to dairy herd management. Automatic milking and feeding robots were used effectively to maintain the performance of milking cows with the improvement of milk quality and the dairy industry capacity. Hence, five working lines with robots in the dairy farm were designed to do smart farming as follows: (1) daily milking line, (2) daily feeding line for milking cows, (3) daily clean up the cow excrement and environmental clean line, (4) cycle management of cow calving and young calf feeding line, and (5) cycle monitoring of cattle health line for cows and heifers. Operations of intelligent milking and/or feeding robots were introduced firstly into breeding farms and then into production farms. A total of 36 dairy farms had robots for feed push, at least 6 times per day with two feedings of total mix rations. Three farms had box-type milking robots and had a greater than 34Kg of daily milk yield by 2.8 milking times per cow with 40~55 cows. Seven farms had milk nursing robots connected with four feeding stations to four groups, 25 newborn calf per station. In summary, the enhancement of automatic operations in dairy cow herds in assistance of the artificial technical components and the intelligent robots had been used to increase precision farming with replacement of aged-labors on the five daily work lines in dairy cattle farms and to ensure sustainable management and a better self-sufficiency rate in tropical Taiwan.
Keywords: Robot, dairy cattle, trait improvement, data analysis
INTRODUCTION
Smart Agriculture 4.0 Program of Taiwan targets three major fields, namely agriculture biotechnology, quality agriculture, and precision agriculture; precision agriculture is divided into two major categories: establishing foundations and promoting excellence. The current technical status of the aforementioned industries and post-promotion applications of the Smart Agriculture 4.0 Program for dairy farm are identified. Hemme and Otto (2010) estimated that 12 to 14% of the world’s population (or 750 to 900 million people) live on dairy farms or within dairy farming households. Livestock provide over half the value of global agricultural output and one-third of this is in developing countries. The United Nations estimates that our world’s population will grow from 7.6 to 9.8 billion between 2017 and 2050 (United Nations, 2017). The world’s population will reach 10.4 billion in 2067 with 81% residing in Africa or Asia (Britt et al., 2018). Britt et al. (2018) stated that dairy farmers in 2067 would meet the world’s needs for essential nutrients by adopting technologies and practices that provide improved cow health and longevity, profitable dairy farms, and sustainable agriculture. Integrated sensors, robotics, and automation would replace much of the manual labor on farms. The fully automatic milking process of the milking robot, which milks the udder on a quarter basis, and the automatic teat-cleaning and milking cup-attachment process have the potential to affect milk variables and udder health. Cows must be motivated to voluntarily approach and enter the milking stall of milking robot, as they are no longer brought to the milking parlor 2 or 3 times daily by human handlers.
PROFITABLE DAIRY FARMING
Significant advances in genetics, milking machines, nutrition, and farm management have combined to create the dairy industry we know today in Japan, EU and USA. For example, the annual milk production per cow in USA has tripled from 2,404 kg in 1953 to 9,049 kg in 2007. In tropical Taiwan, the annual milk production per cow (Figure 1) has improved from 5,308 kg in 1981 to 8,147 kg in 2019 by importation of frozen semen, alfalfa hay and management machinery from Europe and North America (Chang et al., 2001). Due to the general population shifted from small rural villages to larger cities, the need of machine farming for mass-produced and distributed milk products increased not only in Taiwan but also in tropical ASEAN region. The most enticing initial aspect of a milking robot to a farm manager may be relief from the daily milking routine in early morning and evening (Jensen, 2004). Beside the milking routine, on any dairy farm, no matter its size or location, the dairy production technology can be broken down into nine key on-farm activities that can be considered as steps in the supply chain of profitable dairy farming (Moran 2009).
- Soils and forage management: To optimize forage agronomy and fodder conservation.
- Young stock management: To generate productive milking cows.
- Nutrition and feeding management: To optimize cow performance through adequate supplies of feed nutrients.
- Disease prevention and control: To overcome the limits imposed by microbial and invertebrate pests.
- Reproductive management: To ensure herds can replace themselves in future generations.
- Genetics: To maintain an acceptable rate of genetic improvement for each generation.
- Environmental management: To limit the constraints of climate on stock performance.
- Milk harvesting and hygiene: To maximize milk quality pre- and post-farm gate.
- Adding value to milk: To improve unit returns for raw milk.
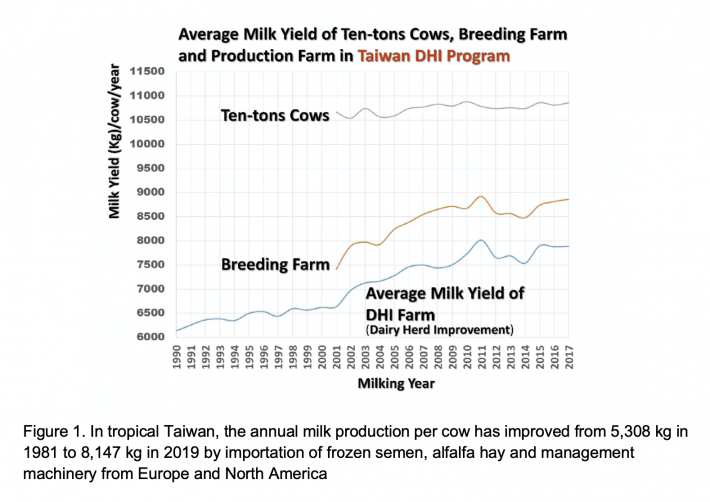
Within the technical research and development, Moran (2013) urged that the supply chain was only as strong as its weakest link. Each step in the supply chain of profitable dairy farming must be properly managed. Weakening any one link through poor decision-making and farming practices can have severe ramifications on overall farm performance and hence profits.
Many of the Southeast Asian dairy industries have recently established large-scale dairy feedlots to provide more milk and so reduce imports of dairy products (Moran and Doyle, 2015). However, these countries all have government-driven development policies for small or medium-sized farms to continue to supply the bulk of locally produced milk. This means existing farms will need to be better managed. Given better farm management and strategic investments, the increased levels of milk produced on such farms should provide sufficient profits–incentives to upgrading current farm management practices. High performing genotype cows require excellent farm management to help them achieve their potential.
Optimized herd management is important for financially successful farming. Both, genetic and environmental improvement, require information collected on farms. The ability to collect data from the dairy farm and transmit to a centralized database under the national DHI (Dairy herd improvement) program has resulted in significant advances in dairy herd management and genetic progress. Traditionally the information was collected on the farm once a month by sending human resources to the farm and either collect data from paper records and key those into a data collection software program, or extract data from the on farm herd management software and load this data into the data collection software program. Several sources of this type of data exist: milk recording, AI (Artificial insemination) organizations, veterinarians, on-farm computer software. By collecting adequate cow fertility and health data for complex analysis of the reproductive status of individuals and herds, it could have the opportunity for genetic evaluation of new functional fertility and health-related traits with higher accuracy and more profitable dairy farming. Due to the growth in the implementation of on farm technology such as robotic milking systems, heat detection systems, feeding systems, etc. the types of data and the frequency by which data becomes available on the farm has rapidly increased. This new data and higher volume of data from herd management assisted technology will further improve the reproductive performance and milk yield of cows in tropical climate.
The animal data exchange working group of ICAR (International Committee for Animal Recording, www.icar.org) leading by Dr. Robert Fourdraine (CRI International Center for Biotechnology, USA) in 2014, had taken on the task of establishing a standardized data interface that can be used by dairy industry partners to connect to on-farm systems extract data and transmit data to a centralized database (ICAR, 2014). Far-east Asian dairy cattle improvement units of Japan, Korea and Taiwan have been the nation member of ICAR since 2011 (Figure 2). None unit of ASEAN is the nation member of ICAR dated in 2019. The standardized data interface is a two-way approach and will enhance value to the farmer and the providers of on-farm systems in addition to those providers with centralized databases. A test platform was established to allow providers of on farm technology and milk recording organizations to test software. Two data flows have been developed one starting at a datacenter to on-farm equipment and one from the on-farm system to a datacenter. Information has been identified that would be beneficial to transmit under both scenarios.
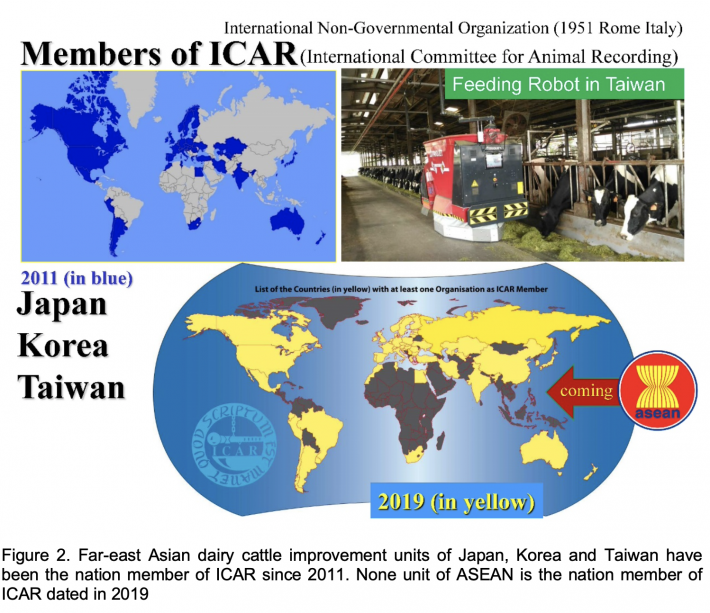
Labor substitute Robots in the dairy farm
Dairy farm has focused on maximizing milk production by replacement of a new milking parlor. Automatic milking systems (AMS) and automatic milking rotary (AMR) parlors are offering the potential for frequent milking events without depending on human labor. One of the greatest changes after installation of milking robot is computerized monitoring, analysis, and control of individual animals in a manner that is transparent to the dairy farmer, and that is substantially advanced beyond conventional milking. The first AMS were installed in the Netherlands in 1992, and by 2009, over 8,000 farms worldwide had adopted AMS of single-box or multi-box (Svennersten-Sjaunja and Pettersson, 2008; de Koning, 2010). Over the past few decades, many changes have occurred in the dairy industry. The introduction of automation in milking has generated a great deal of anticipation for the newest milking advancement in the dairy industry (Jacobs and Siegford, 2012). Robot milking requires a different concept of herd management than conventional milking. The labor routine and the cow behavioral routine are modified substantially with robot milking. Much of the focus of research on milking robot has mirrored consumer interest in milk production, labor, welfare, health, and milk quality. However, a milking robot has the potential to be more than a substitute of equipment for labor. Automatic sensors on milking robot can monitor udder health, milk production, reproductive status, feed intake, and body weight changes to provide detailed information about each cow, which was not easily obtained with labor management and milking systems (Spahr and Maltz, 1997). As a result of big data from automatic sensors, the health and production of individual milking cows can be monitored in greater detail. For example, a milking robot allows the farmer to assess many aspects of cow health, including somatic cell counts in milk, milk color, and electrical conductivity at the level of the udder quarter, which is currently beyond the ability of traditional milking systems. A farm manager who takes advantage of these features of sensor data analysis might be able to detect small changes within the individual cow to more quickly predict illness, as well as be able to watch for trends in overall herd production, potentially allowing for early detection of dietary or disease issues within the herd.
Feeding a totally mixed ration (TMR) where all the ingredients are mixed together and delivered to the cow is conducted in most of conventional herds. The need to reduce labor demand and the increasing size of herds have led to develop specific automated solutions for feeding animals in dairy farms. Currently there are more than 1,250 automatic feeding systems (AFS) used worldwide (Tangorra and Calcante, 2018). Energy consumptions and labor were reduced respectively of 97% and 79% passing from a conventional feeding system (tractor + TMR wagon) to an AFS, contributing to reduce the daily cost for feeding TMR up to 33%. Their results highlighting that AFS can represent an interesting option to improve competitiveness of dairy farms in Italy. Furthermore, AFS can lead to lower energy costs in cattle feeding. Da Borso et al., (2017) reported daily energy consumptions, estimated considering installed power and operation times, reduced of 70 % for an AFS in comparison with a conventional feeding system.
Manure scrapers activated manually or by a timer are widely used in dairy cow loose-housing systems with solid floors. In common, dairy cows perceive the manure-scraping event negatively in some situations, that feeding behavior may be disturbed when scrapers are active during the main feeding period, and that cows avoid the scraper during crowded situations. Two types of manure scrapers are commonly used: straight-bladed scrapers, which span the entire width of the alleyway when moving back and forth; and V-blade scrapers, consisting of two arms that span the alleyway during forward movement and which fold in the middle of the alley during backwards movement. The design and shape of both scraper types vary between manufacturers, but V-blade scrapers are typically not as tall as straight-blade scrapers (Buck et al., 2013). How robotic scraper is helping reduce disease on dairy farm. Impact of robot scrapers on clinical mastitis and somatic cell count in lactating cows was carried out in Germany (Doerfler et al., 2018). They demonstrated that the incidence of clinical mastitis in dairy cattle decreased as a result of automated cleaning of walkways by robot scrapers and thus had a positive effect on udder health. Robot scrapers are increasingly used to remove manure from slatted floors and to improve the cleanliness of walking alleys. Following different routes, these battery-driven machines push the manure deposited on the floor surface down through the slats. In the face of the current demand to reduce antimicrobial drugs in dairy production, the improvement of environmental hygiene becomes increasingly important. The positive impact on udder health is attributable to the cleaner surfaces of walking areas due to robot scraper operation. Maintain a cleaner barn while reducing labor costs with automated slurry robots. Robot scrapers use sensor technology that allows them to scrape and clean manure alleys, in tight spaces, and even between cows.
Five working lines of ROBOTS in Taiwan
The construction of milk production monitoring intelligent system and robotic milking operation parameterized wisdom network were carried out for the study of development and application of pilot robotics in Taiwan since 2017 (Figure 3). Five working lines with robots in the dairy farm were designed to do smart farming as follows: (1) daily milking line, (2) daily feeding line for milking cows, (3) daily clean up the cow excrement and environmental clean line, (4) cycle management of cow calving and young calf feeding line, and (5) cycle monitoring of cattle health line for cows and heifers. Automatic milking and feeding robots were used effectively to maintain the performance of milking cows with the improvement of milk quality and the dairy industry capacity. Enhancement of automatic operations in dairy cow herds in assistance of the artificial technical components and the intelligent robots could be used to increase precision farming with replacement of aged-labors on the five daily work lines of dairy farming (Figure 4).
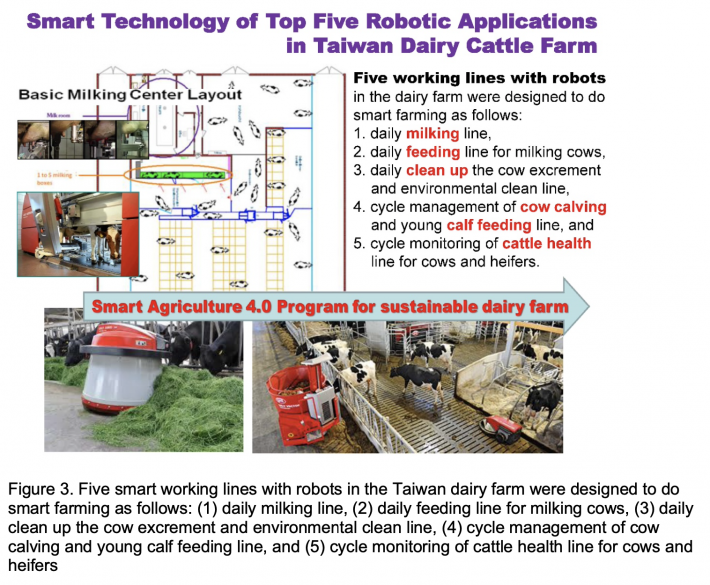
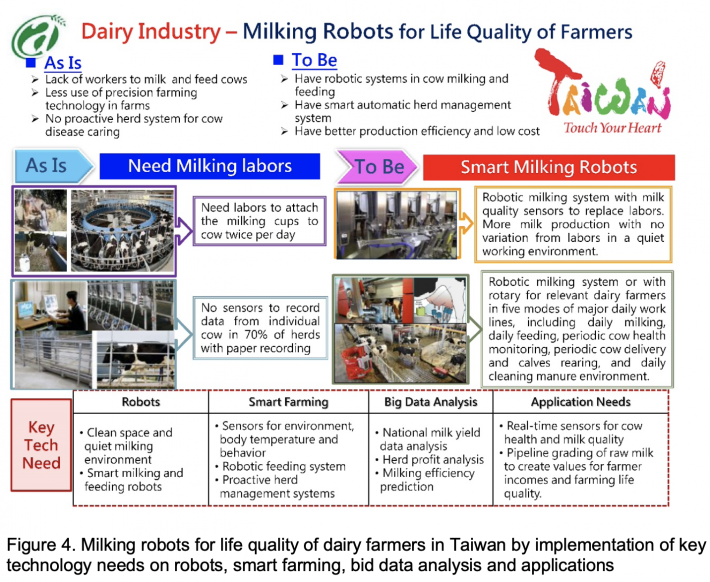
Based upon the performance data of Taiwan dairy herd improvement program (DHI) since 1978, an average of daily milk yield per head was 25.1 kg from 28,485 cows of 177 farms in 2018. Cow raw milk of DHI herds had the quality in average of 3.96% fat, 3.37% protein, 4.79% lactose, and somatic cell counts of 273 thousand cells/mL in 2018. DHI cows were 46.3% of 61,336 milking cows and DHI herds were 32.1% of 551 dairy cattle farms in Taiwan. With a mean of 112 milking cows per herd, dairy farmers will be modernized by application of automatic machinery to manage the cows. Due to lack of young labors and enlargement of herd size, precision farming with robots is becoming an essential to dairy herd management.
TOP REPRODUCTIVE PERFORMANCE COWS
In Taiwan, Ten Tons Cow is designated as milk yield of 305-2X-ME greater than 10,000 kg for hot and humid environment. Dairy cows with trait performance records and genotyping information in Taiwan DHI program have being promoted to improve production efficiency of dairy farms and to have next generation heifers from Ten Tons Cows, which had genes for adaptation to hot and high humidity weather. For breeding scheme of dairy cattle, selection on milk yield and quality associated with reproductive performance is essential to the hot and humid weather, and therefore selected cows will become a heat-tolerance line for Southeast Asia. In 2001, there were 32 test-off Ten Tons Cow (0.1% to 28,381 cows for milk test), and then number of cows up to 103 head in 2002, 146 head in 2003, 254 head in 2004, and 312 head (0.8% to 37,820 cows for milk test) in 2005. An increment of 9 times (312/32) for the number of ten tons cows for the past five years. From 2001 to 2005, age of test-off Ten Tons Cow were 52, 57, 50, 56, and 55 months old, respectively; along with breeding value on milk yield (BVM) of +1113, +988, +1051, +960, +949 kg; and on fat yield (BVF) of +41, +32, +40, +34, +35 kg, respectively. In 2006, there were 1,135 head of Ten Tons Cow (3.4% to 33,064 cows for milk test) with BVM of +894 kg and BVF of +33 kg. Those of Ten Tons Cow were raised in 150 farms (51.2% to 293 testing farms) and among of 40 farms (40/293=13.7%) having more than 10 cows with a total of 797 head (70.22% to 1135 head). In 2018, there were 3,239 test-off Ten Tons Cow (11.3% to 28,542 cows in test) in 142 herds (78.5% of 181 DHI farms). Over 75% of Taiwan DHI farms have focused on data recording and analysis from monthly to daily with automation sensors of milking robot and other machinery. Hence, those of dairy farms having top reproductive performance cows should be managed with daily recording in automation on their milk yield and quality associated with reproductive performance.
CONCLUSION
A lot of people think robots are going to get dairy farmers away from the cows; in fact, it is the complete opposite. If anything, dairy farmers will be more involved with their cows. Before the installation of milking robots most of dairy farmers knew the cows by their udder or back end. Now, they know every cow as soon as they see them approaching the farmer or appointed manager on the dairy barn and/or pasture roadway. The robot via mobile phone tells you so much about each individual cow. Due to the growth in the implementation of on farm technology such as robotic milking systems, heat detection systems, feeding systems, etc. the types of big data and the recording frequency by which big data becomes available on the farm has rapidly increased.
REFERENCES
Britt, J.H., R.A. Cushman, C.D. Dechow, H. Dobson, P. Humblot, M.F. Hutjens, G.A. Jones, P.S. Ruegg, I.M. Sheldon and J.S. Stevenson. 2018. Invited review: Learning from the future—A vision for dairy farms and cows in 2067. Journal of Dairy Science, 101(5): 3722-3741.
Buck, M., K. Friedli, B. Steiner, L. Gygax, B. Wechsler and A. Steiner. 2013. Influence of manure scrapers on dairy cows in cubicle housing systems. Livestock Science, 158:129-137.
Chang, C. L., C. Y. Tseng, S .J. Lee, J. Y. Chen, Y. C. Huang, S. C. Lee, H. L. Chang and M. C. Wu. 2001. Dairy herd improvement (DHI) program in Taiwan. Taiwan Livestock Research, 34(4), 285-295.
Da Borso F., A. Chiumenti, M. Sigura and A. Pezzuolo. 2017. Influence of automatic feeding systems on design and management of dairy farms. Journal of Agricultural Engineering, 48(1):48-52.
de Koning, K. 2010. Automatic milking—Common practice on dairy farms. Proc. Second North Am. Conf. on Robotic Milking, Toronto, Canada, Precision Dairy Operators, Elora, Canada, pp. V59-V63.
Doerfler, R.L., W. Petzl, A. Rieger and H. Bernhardt. 2018. Impact of robot scrapers on clinical mastitis and somatic cell count in lactating cows. Journal of Applied Animal Research, 46(1):467-470.
Hemme, T. and J. Otto. 2010. Status and prospects for smallholder milk production: a global perspective. FAO, Rome.
ICAR. 2014. International Agreement of Recording Practices – ICAR Recording Guidelines. Approved by the General Assembly held in Berlin, Germany, on May 2014, Pp1-637.
Jacobs, J.A. and J.M. Siegford. 2012. Invited review: The impact of automatic milking systems on dairy cow management, behavior, health, and welfare. Journal of Dairy Science, 95(5): 2227-2247.
Jensen, T. 2004. Expectations of automatic milking and the realized socio-economic effects. A.S. Meijering, H. Hogeveen, C.J.A.M. de Koning (Eds.), Automatic Milking—A Better Understanding. Wageningen Academic Publishers, Wageningen, the Netherlands, pp. 78-79.
Moran, J. 2009. Key performance indicators to diagnose poor farm performance and profitability of smallholder dairy farmers in Asia. Asian-Australasian Journal of Animal Sciences 22, 1709-1717.
Moran, J. 2013. Addressing the key constraints to increasing milk production from small holder dairy farms in tropical Asia. International Journal of Agricultural Biosciences 2(3), 90-98.
Moran, J. and R. Doyle. 2015. Cow Talk - Understanding dairy cow behaviour to improve their welfare in Asian farms. CSIRO Publishing, Pp1-256.
Spahr, S.L. and E. Maltz. 1997. Herd management for robot milking. Computers and Electronics in Agriculture, 17(1):53-62.
Svennersten-Sjaunja, K.M. and G. Pettersson. 2008 Pros and cons of automatic milking in Europe. Journal of Animal Science, 86:37-46.
Tangorra, F.M. and A. Calcante. 2018. Energy consumption and technical-economic analysis of an automatic feeding system for dairy farms: Results from a field test. Journal of Agricultural Engineering, 49(4):228-232.
United Nations. 2017. World Population Prospects: The 2017 Revision. Population Division, Department of Economic and Social Affairs, United Nations. https://www.un.org/development/desa/publications/world-population-prospe...
Date submitted: October 24, 2019
Reviewed, edited and uploaded: November 15, 2019 |
Robots for Herd Management of Dairy Cows in Tropical Taiwan
ABSTRACT
Smart Agriculture 4.0 Program of Taiwan targets three major fields, namely agriculture biotechnology, quality agriculture, and precision agriculture; precision agriculture is divided into two major categories: establishing foundations and promoting excellence. The current technical status of the aforementioned industries and post-promotion applications of the Smart Agriculture 4.0 Program for dairy farm are identified. The construction of production monitoring intelligent system and robotic milking operation parameterized wisdom network were carried out for research, development and application of pilot robotics. Based upon the performance data of Taiwan dairy herd improvement program (DHI) since 1978, an average of daily milk yield per head was 25.1Kg from 28,485 cows of 177 farms in 2018. Cow raw milk of DHI herds had the quality in average of 3.96% fat, 3.37% protein, 4.79% lactose, and somatic cell counts of 273 thousand cells/mL in 2018. DHI cows were 46.3% of 61,336 milking cows and DHI herds were 32.1% of 551 dairy cattle farms in Taiwan. Due to lack of young labors and enlargement of herd size, precision farming with robots is becoming an essential to dairy herd management. Automatic milking and feeding robots were used effectively to maintain the performance of milking cows with the improvement of milk quality and the dairy industry capacity. Hence, five working lines with robots in the dairy farm were designed to do smart farming as follows: (1) daily milking line, (2) daily feeding line for milking cows, (3) daily clean up the cow excrement and environmental clean line, (4) cycle management of cow calving and young calf feeding line, and (5) cycle monitoring of cattle health line for cows and heifers. Operations of intelligent milking and/or feeding robots were introduced firstly into breeding farms and then into production farms. A total of 36 dairy farms had robots for feed push, at least 6 times per day with two feedings of total mix rations. Three farms had box-type milking robots and had a greater than 34Kg of daily milk yield by 2.8 milking times per cow with 40~55 cows. Seven farms had milk nursing robots connected with four feeding stations to four groups, 25 newborn calf per station. In summary, the enhancement of automatic operations in dairy cow herds in assistance of the artificial technical components and the intelligent robots had been used to increase precision farming with replacement of aged-labors on the five daily work lines in dairy cattle farms and to ensure sustainable management and a better self-sufficiency rate in tropical Taiwan.
Keywords: Robot, dairy cattle, trait improvement, data analysis
INTRODUCTION
Smart Agriculture 4.0 Program of Taiwan targets three major fields, namely agriculture biotechnology, quality agriculture, and precision agriculture; precision agriculture is divided into two major categories: establishing foundations and promoting excellence. The current technical status of the aforementioned industries and post-promotion applications of the Smart Agriculture 4.0 Program for dairy farm are identified. Hemme and Otto (2010) estimated that 12 to 14% of the world’s population (or 750 to 900 million people) live on dairy farms or within dairy farming households. Livestock provide over half the value of global agricultural output and one-third of this is in developing countries. The United Nations estimates that our world’s population will grow from 7.6 to 9.8 billion between 2017 and 2050 (United Nations, 2017). The world’s population will reach 10.4 billion in 2067 with 81% residing in Africa or Asia (Britt et al., 2018). Britt et al. (2018) stated that dairy farmers in 2067 would meet the world’s needs for essential nutrients by adopting technologies and practices that provide improved cow health and longevity, profitable dairy farms, and sustainable agriculture. Integrated sensors, robotics, and automation would replace much of the manual labor on farms. The fully automatic milking process of the milking robot, which milks the udder on a quarter basis, and the automatic teat-cleaning and milking cup-attachment process have the potential to affect milk variables and udder health. Cows must be motivated to voluntarily approach and enter the milking stall of milking robot, as they are no longer brought to the milking parlor 2 or 3 times daily by human handlers.
PROFITABLE DAIRY FARMING
Significant advances in genetics, milking machines, nutrition, and farm management have combined to create the dairy industry we know today in Japan, EU and USA. For example, the annual milk production per cow in USA has tripled from 2,404 kg in 1953 to 9,049 kg in 2007. In tropical Taiwan, the annual milk production per cow (Figure 1) has improved from 5,308 kg in 1981 to 8,147 kg in 2019 by importation of frozen semen, alfalfa hay and management machinery from Europe and North America (Chang et al., 2001). Due to the general population shifted from small rural villages to larger cities, the need of machine farming for mass-produced and distributed milk products increased not only in Taiwan but also in tropical ASEAN region. The most enticing initial aspect of a milking robot to a farm manager may be relief from the daily milking routine in early morning and evening (Jensen, 2004). Beside the milking routine, on any dairy farm, no matter its size or location, the dairy production technology can be broken down into nine key on-farm activities that can be considered as steps in the supply chain of profitable dairy farming (Moran 2009).
Within the technical research and development, Moran (2013) urged that the supply chain was only as strong as its weakest link. Each step in the supply chain of profitable dairy farming must be properly managed. Weakening any one link through poor decision-making and farming practices can have severe ramifications on overall farm performance and hence profits.
Many of the Southeast Asian dairy industries have recently established large-scale dairy feedlots to provide more milk and so reduce imports of dairy products (Moran and Doyle, 2015). However, these countries all have government-driven development policies for small or medium-sized farms to continue to supply the bulk of locally produced milk. This means existing farms will need to be better managed. Given better farm management and strategic investments, the increased levels of milk produced on such farms should provide sufficient profits–incentives to upgrading current farm management practices. High performing genotype cows require excellent farm management to help them achieve their potential.
Optimized herd management is important for financially successful farming. Both, genetic and environmental improvement, require information collected on farms. The ability to collect data from the dairy farm and transmit to a centralized database under the national DHI (Dairy herd improvement) program has resulted in significant advances in dairy herd management and genetic progress. Traditionally the information was collected on the farm once a month by sending human resources to the farm and either collect data from paper records and key those into a data collection software program, or extract data from the on farm herd management software and load this data into the data collection software program. Several sources of this type of data exist: milk recording, AI (Artificial insemination) organizations, veterinarians, on-farm computer software. By collecting adequate cow fertility and health data for complex analysis of the reproductive status of individuals and herds, it could have the opportunity for genetic evaluation of new functional fertility and health-related traits with higher accuracy and more profitable dairy farming. Due to the growth in the implementation of on farm technology such as robotic milking systems, heat detection systems, feeding systems, etc. the types of data and the frequency by which data becomes available on the farm has rapidly increased. This new data and higher volume of data from herd management assisted technology will further improve the reproductive performance and milk yield of cows in tropical climate.
The animal data exchange working group of ICAR (International Committee for Animal Recording, www.icar.org) leading by Dr. Robert Fourdraine (CRI International Center for Biotechnology, USA) in 2014, had taken on the task of establishing a standardized data interface that can be used by dairy industry partners to connect to on-farm systems extract data and transmit data to a centralized database (ICAR, 2014). Far-east Asian dairy cattle improvement units of Japan, Korea and Taiwan have been the nation member of ICAR since 2011 (Figure 2). None unit of ASEAN is the nation member of ICAR dated in 2019. The standardized data interface is a two-way approach and will enhance value to the farmer and the providers of on-farm systems in addition to those providers with centralized databases. A test platform was established to allow providers of on farm technology and milk recording organizations to test software. Two data flows have been developed one starting at a datacenter to on-farm equipment and one from the on-farm system to a datacenter. Information has been identified that would be beneficial to transmit under both scenarios.
Labor substitute Robots in the dairy farm
Dairy farm has focused on maximizing milk production by replacement of a new milking parlor. Automatic milking systems (AMS) and automatic milking rotary (AMR) parlors are offering the potential for frequent milking events without depending on human labor. One of the greatest changes after installation of milking robot is computerized monitoring, analysis, and control of individual animals in a manner that is transparent to the dairy farmer, and that is substantially advanced beyond conventional milking. The first AMS were installed in the Netherlands in 1992, and by 2009, over 8,000 farms worldwide had adopted AMS of single-box or multi-box (Svennersten-Sjaunja and Pettersson, 2008; de Koning, 2010). Over the past few decades, many changes have occurred in the dairy industry. The introduction of automation in milking has generated a great deal of anticipation for the newest milking advancement in the dairy industry (Jacobs and Siegford, 2012). Robot milking requires a different concept of herd management than conventional milking. The labor routine and the cow behavioral routine are modified substantially with robot milking. Much of the focus of research on milking robot has mirrored consumer interest in milk production, labor, welfare, health, and milk quality. However, a milking robot has the potential to be more than a substitute of equipment for labor. Automatic sensors on milking robot can monitor udder health, milk production, reproductive status, feed intake, and body weight changes to provide detailed information about each cow, which was not easily obtained with labor management and milking systems (Spahr and Maltz, 1997). As a result of big data from automatic sensors, the health and production of individual milking cows can be monitored in greater detail. For example, a milking robot allows the farmer to assess many aspects of cow health, including somatic cell counts in milk, milk color, and electrical conductivity at the level of the udder quarter, which is currently beyond the ability of traditional milking systems. A farm manager who takes advantage of these features of sensor data analysis might be able to detect small changes within the individual cow to more quickly predict illness, as well as be able to watch for trends in overall herd production, potentially allowing for early detection of dietary or disease issues within the herd.
Feeding a totally mixed ration (TMR) where all the ingredients are mixed together and delivered to the cow is conducted in most of conventional herds. The need to reduce labor demand and the increasing size of herds have led to develop specific automated solutions for feeding animals in dairy farms. Currently there are more than 1,250 automatic feeding systems (AFS) used worldwide (Tangorra and Calcante, 2018). Energy consumptions and labor were reduced respectively of 97% and 79% passing from a conventional feeding system (tractor + TMR wagon) to an AFS, contributing to reduce the daily cost for feeding TMR up to 33%. Their results highlighting that AFS can represent an interesting option to improve competitiveness of dairy farms in Italy. Furthermore, AFS can lead to lower energy costs in cattle feeding. Da Borso et al., (2017) reported daily energy consumptions, estimated considering installed power and operation times, reduced of 70 % for an AFS in comparison with a conventional feeding system.
Manure scrapers activated manually or by a timer are widely used in dairy cow loose-housing systems with solid floors. In common, dairy cows perceive the manure-scraping event negatively in some situations, that feeding behavior may be disturbed when scrapers are active during the main feeding period, and that cows avoid the scraper during crowded situations. Two types of manure scrapers are commonly used: straight-bladed scrapers, which span the entire width of the alleyway when moving back and forth; and V-blade scrapers, consisting of two arms that span the alleyway during forward movement and which fold in the middle of the alley during backwards movement. The design and shape of both scraper types vary between manufacturers, but V-blade scrapers are typically not as tall as straight-blade scrapers (Buck et al., 2013). How robotic scraper is helping reduce disease on dairy farm. Impact of robot scrapers on clinical mastitis and somatic cell count in lactating cows was carried out in Germany (Doerfler et al., 2018). They demonstrated that the incidence of clinical mastitis in dairy cattle decreased as a result of automated cleaning of walkways by robot scrapers and thus had a positive effect on udder health. Robot scrapers are increasingly used to remove manure from slatted floors and to improve the cleanliness of walking alleys. Following different routes, these battery-driven machines push the manure deposited on the floor surface down through the slats. In the face of the current demand to reduce antimicrobial drugs in dairy production, the improvement of environmental hygiene becomes increasingly important. The positive impact on udder health is attributable to the cleaner surfaces of walking areas due to robot scraper operation. Maintain a cleaner barn while reducing labor costs with automated slurry robots. Robot scrapers use sensor technology that allows them to scrape and clean manure alleys, in tight spaces, and even between cows.
Five working lines of ROBOTS in Taiwan
The construction of milk production monitoring intelligent system and robotic milking operation parameterized wisdom network were carried out for the study of development and application of pilot robotics in Taiwan since 2017 (Figure 3). Five working lines with robots in the dairy farm were designed to do smart farming as follows: (1) daily milking line, (2) daily feeding line for milking cows, (3) daily clean up the cow excrement and environmental clean line, (4) cycle management of cow calving and young calf feeding line, and (5) cycle monitoring of cattle health line for cows and heifers. Automatic milking and feeding robots were used effectively to maintain the performance of milking cows with the improvement of milk quality and the dairy industry capacity. Enhancement of automatic operations in dairy cow herds in assistance of the artificial technical components and the intelligent robots could be used to increase precision farming with replacement of aged-labors on the five daily work lines of dairy farming (Figure 4).
Based upon the performance data of Taiwan dairy herd improvement program (DHI) since 1978, an average of daily milk yield per head was 25.1 kg from 28,485 cows of 177 farms in 2018. Cow raw milk of DHI herds had the quality in average of 3.96% fat, 3.37% protein, 4.79% lactose, and somatic cell counts of 273 thousand cells/mL in 2018. DHI cows were 46.3% of 61,336 milking cows and DHI herds were 32.1% of 551 dairy cattle farms in Taiwan. With a mean of 112 milking cows per herd, dairy farmers will be modernized by application of automatic machinery to manage the cows. Due to lack of young labors and enlargement of herd size, precision farming with robots is becoming an essential to dairy herd management.
TOP REPRODUCTIVE PERFORMANCE COWS
In Taiwan, Ten Tons Cow is designated as milk yield of 305-2X-ME greater than 10,000 kg for hot and humid environment. Dairy cows with trait performance records and genotyping information in Taiwan DHI program have being promoted to improve production efficiency of dairy farms and to have next generation heifers from Ten Tons Cows, which had genes for adaptation to hot and high humidity weather. For breeding scheme of dairy cattle, selection on milk yield and quality associated with reproductive performance is essential to the hot and humid weather, and therefore selected cows will become a heat-tolerance line for Southeast Asia. In 2001, there were 32 test-off Ten Tons Cow (0.1% to 28,381 cows for milk test), and then number of cows up to 103 head in 2002, 146 head in 2003, 254 head in 2004, and 312 head (0.8% to 37,820 cows for milk test) in 2005. An increment of 9 times (312/32) for the number of ten tons cows for the past five years. From 2001 to 2005, age of test-off Ten Tons Cow were 52, 57, 50, 56, and 55 months old, respectively; along with breeding value on milk yield (BVM) of +1113, +988, +1051, +960, +949 kg; and on fat yield (BVF) of +41, +32, +40, +34, +35 kg, respectively. In 2006, there were 1,135 head of Ten Tons Cow (3.4% to 33,064 cows for milk test) with BVM of +894 kg and BVF of +33 kg. Those of Ten Tons Cow were raised in 150 farms (51.2% to 293 testing farms) and among of 40 farms (40/293=13.7%) having more than 10 cows with a total of 797 head (70.22% to 1135 head). In 2018, there were 3,239 test-off Ten Tons Cow (11.3% to 28,542 cows in test) in 142 herds (78.5% of 181 DHI farms). Over 75% of Taiwan DHI farms have focused on data recording and analysis from monthly to daily with automation sensors of milking robot and other machinery. Hence, those of dairy farms having top reproductive performance cows should be managed with daily recording in automation on their milk yield and quality associated with reproductive performance.
CONCLUSION
A lot of people think robots are going to get dairy farmers away from the cows; in fact, it is the complete opposite. If anything, dairy farmers will be more involved with their cows. Before the installation of milking robots most of dairy farmers knew the cows by their udder or back end. Now, they know every cow as soon as they see them approaching the farmer or appointed manager on the dairy barn and/or pasture roadway. The robot via mobile phone tells you so much about each individual cow. Due to the growth in the implementation of on farm technology such as robotic milking systems, heat detection systems, feeding systems, etc. the types of big data and the recording frequency by which big data becomes available on the farm has rapidly increased.
REFERENCES
Britt, J.H., R.A. Cushman, C.D. Dechow, H. Dobson, P. Humblot, M.F. Hutjens, G.A. Jones, P.S. Ruegg, I.M. Sheldon and J.S. Stevenson. 2018. Invited review: Learning from the future—A vision for dairy farms and cows in 2067. Journal of Dairy Science, 101(5): 3722-3741.
Buck, M., K. Friedli, B. Steiner, L. Gygax, B. Wechsler and A. Steiner. 2013. Influence of manure scrapers on dairy cows in cubicle housing systems. Livestock Science, 158:129-137.
Chang, C. L., C. Y. Tseng, S .J. Lee, J. Y. Chen, Y. C. Huang, S. C. Lee, H. L. Chang and M. C. Wu. 2001. Dairy herd improvement (DHI) program in Taiwan. Taiwan Livestock Research, 34(4), 285-295.
Da Borso F., A. Chiumenti, M. Sigura and A. Pezzuolo. 2017. Influence of automatic feeding systems on design and management of dairy farms. Journal of Agricultural Engineering, 48(1):48-52.
de Koning, K. 2010. Automatic milking—Common practice on dairy farms. Proc. Second North Am. Conf. on Robotic Milking, Toronto, Canada, Precision Dairy Operators, Elora, Canada, pp. V59-V63.
Doerfler, R.L., W. Petzl, A. Rieger and H. Bernhardt. 2018. Impact of robot scrapers on clinical mastitis and somatic cell count in lactating cows. Journal of Applied Animal Research, 46(1):467-470.
Hemme, T. and J. Otto. 2010. Status and prospects for smallholder milk production: a global perspective. FAO, Rome.
ICAR. 2014. International Agreement of Recording Practices – ICAR Recording Guidelines. Approved by the General Assembly held in Berlin, Germany, on May 2014, Pp1-637.
Jacobs, J.A. and J.M. Siegford. 2012. Invited review: The impact of automatic milking systems on dairy cow management, behavior, health, and welfare. Journal of Dairy Science, 95(5): 2227-2247.
Jensen, T. 2004. Expectations of automatic milking and the realized socio-economic effects. A.S. Meijering, H. Hogeveen, C.J.A.M. de Koning (Eds.), Automatic Milking—A Better Understanding. Wageningen Academic Publishers, Wageningen, the Netherlands, pp. 78-79.
Moran, J. 2009. Key performance indicators to diagnose poor farm performance and profitability of smallholder dairy farmers in Asia. Asian-Australasian Journal of Animal Sciences 22, 1709-1717.
Moran, J. 2013. Addressing the key constraints to increasing milk production from small holder dairy farms in tropical Asia. International Journal of Agricultural Biosciences 2(3), 90-98.
Moran, J. and R. Doyle. 2015. Cow Talk - Understanding dairy cow behaviour to improve their welfare in Asian farms. CSIRO Publishing, Pp1-256.
Spahr, S.L. and E. Maltz. 1997. Herd management for robot milking. Computers and Electronics in Agriculture, 17(1):53-62.
Svennersten-Sjaunja, K.M. and G. Pettersson. 2008 Pros and cons of automatic milking in Europe. Journal of Animal Science, 86:37-46.
Tangorra, F.M. and A. Calcante. 2018. Energy consumption and technical-economic analysis of an automatic feeding system for dairy farms: Results from a field test. Journal of Agricultural Engineering, 49(4):228-232.
United Nations. 2017. World Population Prospects: The 2017 Revision. Population Division, Department of Economic and Social Affairs, United Nations. https://www.un.org/development/desa/publications/world-population-prospe...
Reviewed, edited and uploaded: November 15, 2019